Product update – pump efficiency monitoring
Over the past two to three years, energy prices have reached unprecedented levels.
In industrial companies, 45 percent of their electrical energy use is for motors driving pumps and other equipment. Pipelines are the most efficient and safest way of moving fluids from one point to another, but here the percentage of energy used is even more significant. Improving the efficiency of pipeline pumps is therefore the most effective way of reducing energy consumption and improving CO2 footprint.
To address this, Klarian offers one of the most sought-after solutions in the pipeline monitoring industry: pump efficiency monitoring.
Traditional efficiency monitoring systems provide a broad overview of energy consumption across sites or businesses. They highlight energy usage patterns, identify which assets consume the most energy, and offer insights into overall energy consumption.
However, the efficiency of a pump is also affected by its installation and the remainder of the pipeline that it is serving.
Klarian therefore takes this a step further. We provide a view that enables pipeline operators to build a picture of how they are using their assets, how they can save energy, improve throughput and reduce their carbon footprint. We achieve this by characterising each pump using manufacturer data and monitoring its operation relative to this reference, along with usage patterns and throughput and energy use.
Next month, we will delve deeper into an additional layer of our monitoring solution. This will involve analysing entire pipeline legs or routes, factoring in delivery timings, energy savings, and overall pumping effectiveness. However, for now, we are focusing on individual pumps.
We begin with an initial analysis, generating reports that cover pump efficiency and utilisation over time, based on historical data. These reports include graphical demonstrations of pump operations and proposals for potential improvements, such as optimal pumping times and better pump-system matches.
Using this baseline, our cloud-enabled DigipipeVision software provides a real-time view of pump operations. This ensures that customers can quickly spot changes in pump efficiency, identify areas for operational improvements, and receive early warnings of potential maintenance needs.
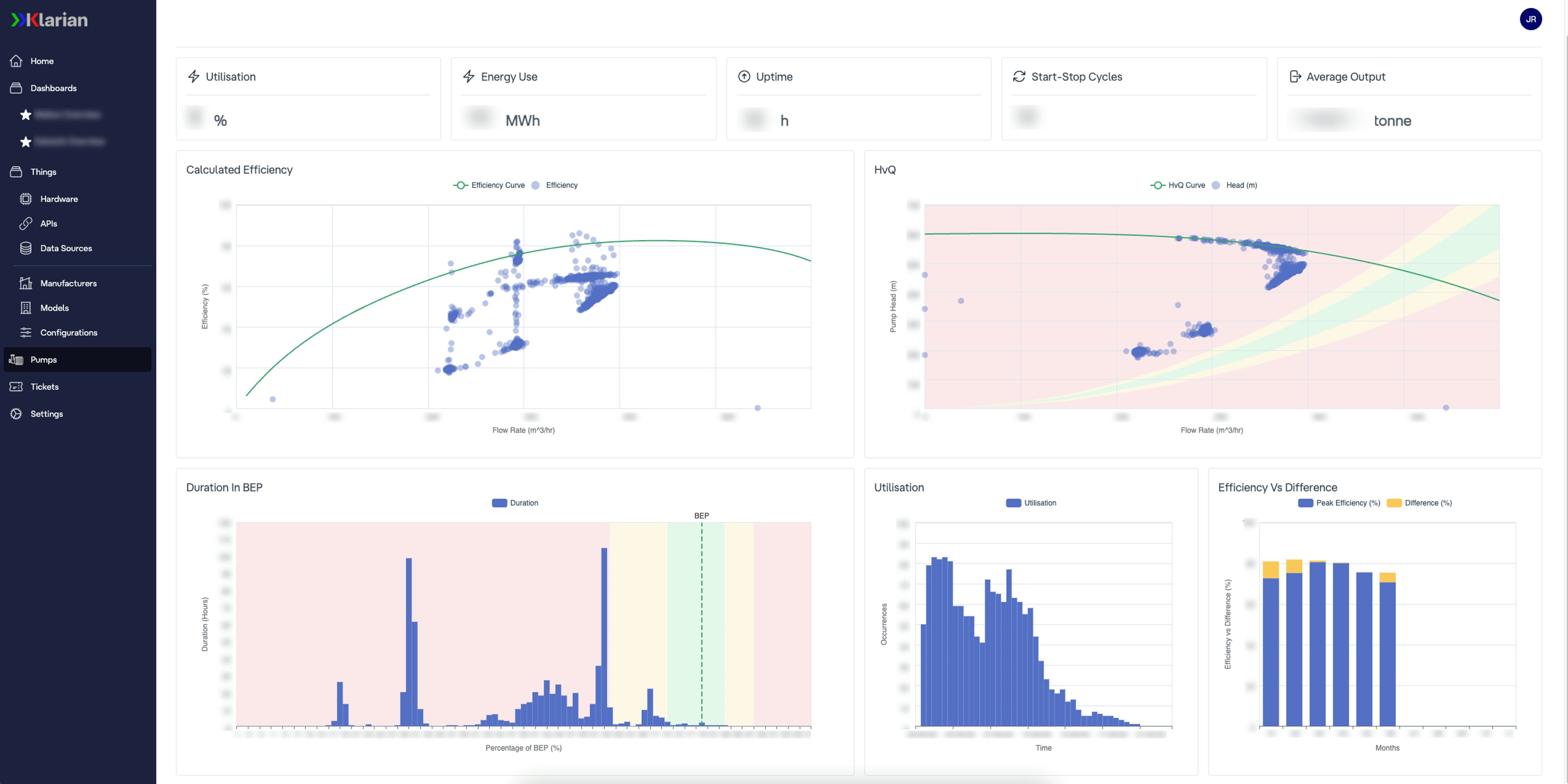
BPA, one of the UK’s foremost onshore pipeline operators are working with us to maximise throughput and efficiency, whilst making significant energy and cost savings. Is this functionality something you also need? Please contact us to discuss how we can help you make your pumps more efficient, reduce their carbon footprint, and save on operating costs while improving overall operations.
*The BEP or best efficiency point is the flow rate at which a pump operates at its greatest efficiency. HvQ curves plot the head against the flow rate for a pump over time, referencing it against the ideal operating curve for that pump.