The origins of predictive maintenance in aviation and how it’s applied in the pipeline industry today
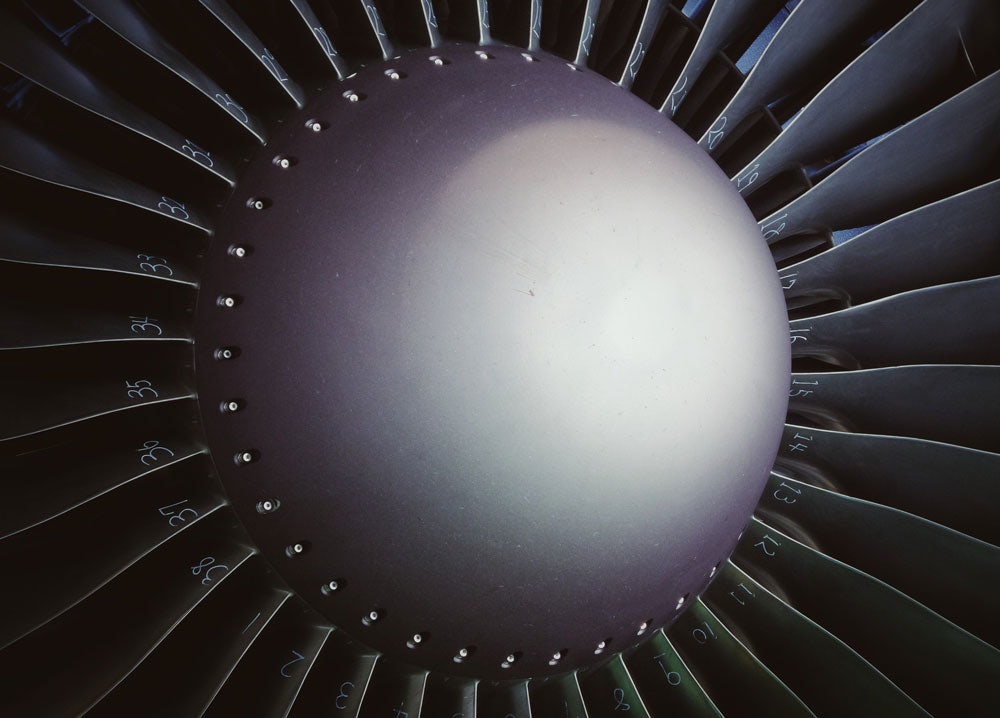
Predictive maintenance is about being able to spot that something is going to malfunction and fixing it before it does. It is the pinnacle of maintenance regimes. Predictive maintenance harnesses data to analyse and predict when your equipment or assets are going to fail. It is a more proactive, cost-effective and efficient method of upkeep than simply making repairs when something goes wrong.
If you predict when something is going to break and replace it before it does, you will save money and time. It is why you should act sooner rather than later if a warning light comes on in your car. Topping up your engine oil is a lot cheaper and quicker than having to replace the entire engine. Predictive maintenance would predict exactly when a warning light would appear in your car and for what reason.
Predictive maintenance solutions are one way you can increase your operational efficiency and reduce costs.
Predictive maintenance and aviation
The aviation industry has always had high operating and maintenance costs. If an aircraft is grounded for an unexpected reason, the financial and personal costs can be huge for both the passengers and the airline. It is why predictive maintenance originated within the aviation industry.
Originally, aviators believed that all aircraft and their components had a set lifetime of use after which they should be replaced. In short, more maintenance meant fewer issues. Unfortunately, maintenance does not always equal efficiency.
Research undertaken during the Second World War challenged conventional views and the first occurrences of predictive maintenance uses within aviation. The RAF observed that their B-24 Liberators were spending a lot of time grounded for both scheduled and unscheduled maintenance. The RAF Coast Command tasked a British scientist, C.H. Waddington, to investigate why. Waddington and his team took the following steps:
- Gathered and analysed as much data as they could.
- Identified that unscheduled repairs increased dramatically after scheduled maintenance.
- Concluded that scheduled maintenance caused breakdowns.
Ironically, the planned maintenance schedules had the opposite of their intended purpose and caused downtime – a phenomenon now known as ‘The Waddington Effect’. The solution was to base the maintenance schedules upon the condition of the equipment and how often it was used rather than age.
Waddington laid the groundwork for predictive maintenance and aviation. A couple of decades later in the 1960s, research conducted by United Airlines (UAL) reached the same conclusion. Waddington’s and UAL’s work mean that condition-based monitoring (a particular kind of predictive maintenance) is now standard within the aviation industry.
Rolls Royce and predictive maintenance
Predictive maintenance best practices continue to exist within the aviation industry. Today, predictive maintenance techniques are getting more and more sophisticated with the arrival of Industry 4.0. While Rolls Royce may be most famous for their cars, Rolls Royce engines also power 35 types of commercial aircraft.
Rolls Royce and predictive maintenance in the aviation industry are now intrinsically linked. Rolls Royce uses the Internet of Things (IoT) to collect and analyse data that helps identify and predict maintenance needs. Parts are only replaced when necessary and aircraft downtime is reduced, saving cost, and increasing efficiency.
Predictive maintenance and the pipeline industry
While predictive maintenance originated within the aviation industry, its uses are far-reaching. As with planes, if a pipeline is out of action for an extended period, the financial and personal costs can be huge.
Asset condition monitoring and predictive maintenance help operators understand how their assets are performing so they can identify and treat anomalies before they mature into incidents or downtime. Klarian can provide these services for you by tracking machinery health and vibration. We build bespoke analytics models to provide condition-monitoring solutions for motors, bearings, pumps and compressors. Read more about our solutions for asset optimisation to learn more.