How system-level modelling can optimise pipeline pumps and compressors
We repeatedly mention how important pumps and compressors are when you’re thinking about optimising your operations.
After we speak with you, analysing your pump and compressor data is often our first step towards identifying efficiency gains. In this article, we delve into why these assets are critical and how we use our AI and human analytics expertise to increase your productivity, profitability, and cost-efficiency.
We published an article on this in the October 2023 edition of World Pipelines Magazine – “Green and Lean: Data Driven Asset Optimisation for Transmission Pipelines”. The following is an edited extract, and you can get your hands on the entire article at the bottom.
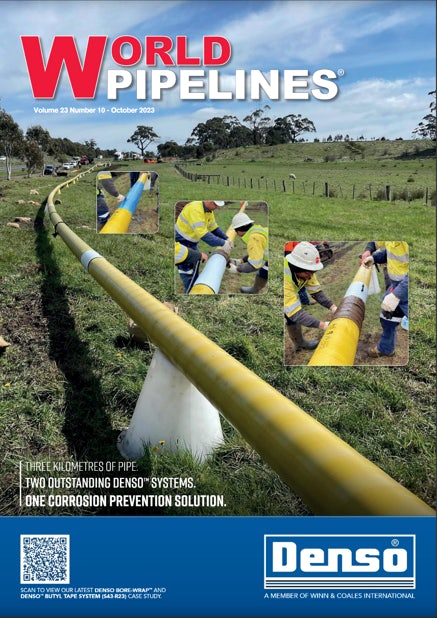
World Pipelines, October 2023
Pipeline pumps and compressors: pillars of the energy industry
Pumps and compressors are the mechanical workhorses of pipeline infrastructure, ensuring a steady flow of hydrocarbons through the vast networks of large-diameter transmission pipelines spanning the globe. The challenge operators face is that pumps and compressors, at scale, are energy-intensive machines. The US Department of Energy’s Office of Industrial Technologies (OIT) reported that pumping systems account for 20-25% “of the energy usage in certain industrial plant operations.” High electricity usage generates high operating costs and carbon emissions. Over time, these increase with the everyday wear and tear of equipment, decreasing efficiency and causing unplanned downtime, further harming productivity and profitability.
We cannot overstate the importance of pumps and compressors, so optimising these assets should top the list of areas operators are looking to improve. The industry must harness new data-driven technologies to take care of and improve the use of these vital assets.
Systems level modelling for pipeline pump and compressor optimisation
The performance of pumps and compressors depends highly upon the system they are a part of. A carefully designed system with optimally sized pumps may change significantly over time due to changes in pumped products, asset degradation/renovation, expansions, closures within the network, and much more. A system with multiple routes from source to destination may also require certain compromises.
Pump and compressor optimisation is ideally performed for each experienced system curve. For complete analysis, data must be sorted based on each system curve encountered. Presently, this process involves valuable but laborious automation, necessitating semi-bespoke software to scrutinise an array of data – including flow, pressure, density, and valve status – to pinpoint these instances. Given AI's pattern recognition abilities, it would not be a stretch to imagine AI algorithms capable of interpreting P&IDs and parsing SCADA could be trained to identify, sort, and calculate all the system curves each asset experiences in near-real-time.
Once the operational conditions are understood, analytical means can compute various beneficial metrics. Most critical for optimisation would be the HvQ curves for each operational condition, and their associated energy-per-volume and average-throughput statistics. Armed with this information, it becomes a classic engineering challenge to decide on optimisation techniques, such as drag reduction agents, changes to RPM profiles, or asset refurbishment/replacement.
The benefits of pump optimisation are clear. If you know the optimal route or time to pump, you can lower energy usage and reduce operating costs all the while maximising productivity, throughput and profitability. It’s a core offering within our Digipipe service.
If this caught your attention, you could get our whole article as featured in World Pipelines sent directly to your inbox by signing up below: